
4 - Component placement methods
4.3 Feeder types
It is important to feed the insertion machines continuously with components during mounting thus, therefore special feeders are used. The most commonly used feeders are the tape and reel feeders. Width of the tape is 8–72 mm, made of plastic or paper. It is perforated on one side for stepping. Components (3 000 – 5 000 pieces) are in dies, covered with plastic strip. Tapes are stored on reels (diameter 178–381 mm). Tapes are inserted into tape feeders, that move the tape and removes the cover strip. Feeders can be changed, and they are modular.
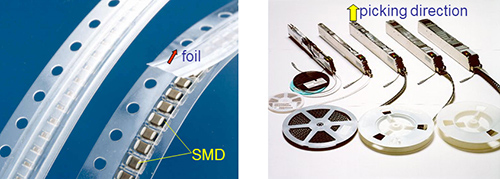
Tape feeders
The basic construction of a tape feeder is shown in figure. Tape is unrolled from the reel into the module, where the cover strip is pulled off so that the components at the pick-up position can be lifted out by the placement head. The cover strip pulled off is wound onto a small collecting reel. The remaining empty tape runs back out of the module. After the placement head has removed the component, the tape is indexed one increment further so that the next component can be removed at the pick-up position.
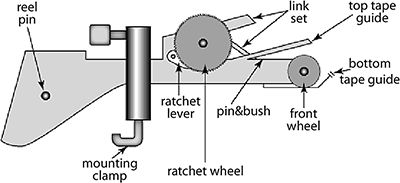
Stick magazines
Stick magazines are plastic or metal tubes. Feeders are vibrating in order to move the components. Considerable disadvantage is the low capacity. Mostly packaged IC-s are stored in stick magazines.
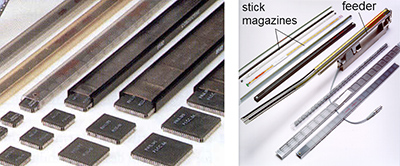
Tray magazines
The tray format of component presentation, commonly known as the ‘waffle-pack’ method, is used primarily to feed large components and those with fine lead pitches. Such trays were first seen with the introduction of QFP and DIL style devices. Waffle trays are generally available in sizes of 25.4 mm × 25.4 mm and larger. There are also large vacuum formed packs, as large as 305 mm × 508 mm, used for flat-pack type devices. The individual internal component recesses of these trays are made to conform to the size of individual parts. As a result, a wide variety of tray sizes is available. Goods inwards handling and storage are not a real problem, but once the trays are made ready for machine loading, in-house transportation and handling become a major concern in order to prevent component loss or damage.
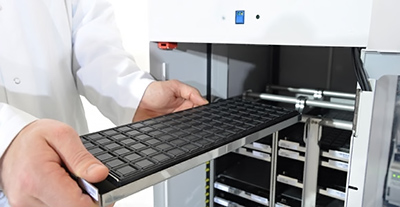
Placement machines using waffle-trays have to divert their placement sequence to place other components during the time that waffle tray changeover is taking place. This can lead to an unnecessary increase in cycle times if the number of QFP component types is high. A cassette magazine can be installed which reduces the down-time for component replenishment. Components on waffle-trays place considerable demands on the flexibility of any surface mount pick and place system since they require a lot of space and automatic handling systems if they are to process a large number of different component types and eliminate down time for tray replacement. Equipment with tray feeder towers, and able to handle large components, tends to involve a pretty substantial investment in space, as well as in capital!
The advantages of tray feeders are:
- All components are individually packaged
- The packaging is usually stiff, therefore there is no bending as with tapes
The disadvantages are:
- Small number of components per tray, requiring frequent tray exchange
- More complex logistics when using partly filled trays
- Components can be removed from the tray manually, with the chance of wrong component or component orientation
- More expensive types of packaging (sometimes returnable)
- Trays must be handled carefully, as components will shift if subjected to sudden movements, which may result in mis-picks or damaged leads
Feeding placement machines
By contrast with through-hole components, parts for surface mounting use just a single placement method, where the part is removed from its carrier by a vacuum tool, carried to the intended location, and pressed lightly into the solder paste. Whilst many types of machines are used, they all have the same requirement, which is to have the component presented in a known position relative to its packaging. Because surface mount assembly is favoured for being a fast operation, suppliers have gone to such extreme lengths that even the most apparently unsuitable parts are now packaged in one of the standard forms. The feeder modules are placed close side by side. They can simultaneously be changed with a small vehicle (one machine may have more vehicles). These processes make easier to switch the manufacturing from one to another product.
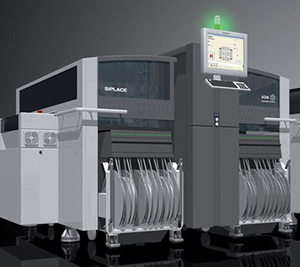
Previous | Next |