
5 - Reflow soldering ovens and reflow profiling
5.1 - Heat transport methods and reflow ovens
Heat transfer modes
Soldering is the process in which two metals are joined together by means of a third metal or alloy having a lower melting point. Soft soldering is characterized by the value of the melting point of the third metal or alloy, which is below 400 °C. The third metal or alloy used in the process is called solder. Heat transport is necessary to heat up the assembly, to activate the flux to melt the solder and to form the solder joint. The three fundamental modes of heat transfer are:
- Conduction
- Convection
- Radiation
Conduction
Thermal conduction is the transfer of heat (internal energy) by microscopic collisions of particles and movement of electrons within a body. The rate at which energy is conducted as heat between two bodies is a function of the temperature difference (temperature gradient) between the two bodies and the properties of the conductive medium through which the heat is transferred. The law of heat conduction (Fourier's law) states that the time rate of heat transfer through a material is proportional to the negative gradient in the temperature and to the area, at right angles to that gradient, through which the heat flows.
where is the local heat flux density (W·m−2), is the material's conductivity (W·m−1·K−1), and is the temperature gradient (K·m−1). For many simple applications, Fourier's law is used in its one-dimensional form. In the x-direction:
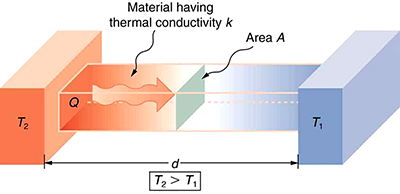
Convection
Convective heat transfer, often referred to simply as convection, is the transfer of heat from one place to another by the movement of fluids. Convection can be "forced" by movement of a fluid by means other than buoyancy forces (for example, forcing air to flow by fans). Thermal expansion of fluids may also force convection. In other cases, natural buoyancy forces alone are entirely responsible for fluid motion when the fluid is heated, and this process is called "natural convection".
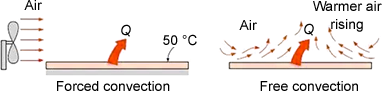
The basic relationship for heat transfer by convection is:
where is the heat transferred per unit time, is the area of the object, is the heat transfer coefficient, is the object's surface temperature, and is the fluid temperature. The convective heat transfer coefficient is dependent upon the physical properties of the fluid and the physical situation.
Radiation
Infrared radiation (IR) is electromagnetic radiation (EMR) with longer wavelengths than those of visible light. It extends from the nominal red edge of the visible spectrum at 780 nanometers to 1000 µm. Infrared radiation is emitted or absorbed by molecules when they change their rotational-vibrational movements. Fluxes, plastic components, and epoxy glass laminates absorb IR very well. Shiny surfaces, like metals, solder joints will reflect the IR energy away.
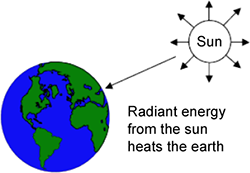
The Stefan–Boltzmann law describes the thermal energy radiated by a blackbody radiator. If the hot object (grey body, which emits less total energy than a blackbody radiator) is radiating energy to its cooler surroundings, the expression takes the form:
where is the energy transferred per unit time, is the Stefan-Boltzmann constant (5.67 × 10-8
W·m-2K-4), is the emissivity of the grey body, which depends on the wavelength (if the hot body is a perfect blackbody, ), is the area of the object, is the temperature of the radiator, and is the temperature of the surrounding.
W·m-2K-4), is the emissivity of the grey body, which depends on the wavelength (if the hot body is a perfect blackbody, ), is the area of the object, is the temperature of the radiator, and is the temperature of the surrounding.
Wetting of the solder
The wetting means the spreading of the heated and melted solder on the contact surfaces. The solderability of a surface is defined by its solder wetting characteristics. Solder wetting pertains to the formation of a relatively uniform, smooth, and unbroken film of solder that exhibits excellent adherence on the soldered surface. Non-wetting, on the other hand, is the condition wherein the solder coating has contacted the surface but did not adhere completely to it, causing the surface or a part thereof to be exposed. Dewetting is the condition wherein the solder recedes after coating a surface, creating irregular mounds of solder, but leaving behind no exposed areas. Suitable wetting needs to the joint formation.
The contact angle is the angle, conventionally measured through the liquid, where a liquid–vapor interface meets a solid surface. It quantifies the wettability of a solid surface by a liquid via the Young equation:
where is the solid–vapor interfacial energy, is the solid–liquid interfacial energy, is the liquid–vapor interfacial energy, and is the wetting angle. Rearranging this to make the wetting angle the subject:
which implies that the wetting angle depends on the material properties of the molten alloy plus the solder pad and on the atmosphere of the reflow oven (can be air or nitrogen). Further conclusion can be drawn: lower means lower wetting angle and better wetting.
Reflow profile
Thermal profile (the way of the heating) means the temperature of the assembly as a function of time.
The ΔT is the highest temperature difference between different locations (components) of the assembly in the same moment during the soldering.
Process Window is a temperature range – the peak temperature of all components should lie within it.
The ΔT is the highest temperature difference between different locations (components) of the assembly in the same moment during the soldering.
Process Window is a temperature range – the peak temperature of all components should lie within it.
The applied reflow profile (soak or linear) depends on the size and complexity of the circuit board. The advantage of linear profile is its duration; because the soak section is eliminated, therefore the profile is shorter by 30 to 60 seconds. Linear thermal profiles are used in the cases, when the temperature difference between the components (ΔT) during soldering is in acceptable level. Usually used for circuits, where the components are in nearly the same size and mass.
When the difference in the heat capacity of the components and thus the difference in their peak temperature components is larger, soak reflow profiles are used. The role of the soak section is to lower the distribution in the temperature between the components.
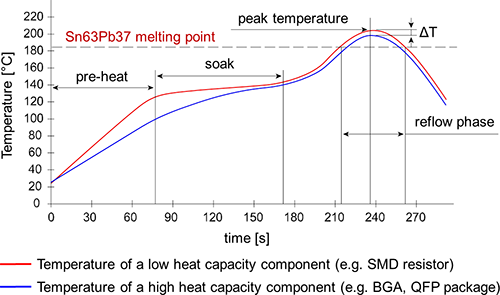
The soak profile can be divided into five zones: pre-heat, pre-flow or soak, ramp-up, reflow, and cool down. During the pre-heat phase, the solvents evaporate from the solder paste. If the temperature rises during the pre-heat too rapidly or two slowly, two failures can occur. First, solder particles can be spread when the solvents burst through the flux surface membrane. This is called solder beading. Second, the solder paste can slump, because of a too slow temperature rise. This will result in bridging. A typical preheat phase has a slope of 0.5–1.0 °C/s.
The pre-flow or soak and the ramp-up section, also called the flux activation stage, brings the entire assembly up to the temperature at which the flux activating and the alloy in the paste changes its phase from solid to liquid. This soak time should be long enough to allow the flux to clean the surfaces, but not so long that the flux is evaporated prematurely.
During the reflow phase, the temperature increases further to melt the solder alloy and subsequently, intermetallic layer will form at the boundary surfaces. The typical peak temperature is 30–40 °C higher than the solder alloy melting point. It is important to monitor the time at peak reflow temperature in several areas of the PCB.
In the cool down phase, a reliable solder joint is formed. To obtain a strong joint between the solder pad and the components' terminal, the cooling should be fast. A lower rate may increase the grain size of the intermetallic compounds making the solder joint brittle and weak. On the other hand, the components can crack if the temperature drops too rapidly. The cooling rate should therefore be 3–4 °C/s down to around 130 °C. Below 130 °C the cooling rate is not critical to the solder joint quality; however fast cooling is beneficial for copper OSP board rather than a very slow cooling rate. The solderability will be maintained for second side reflow, wave or selective soldering. Conveyor speed is a critical affecting parameter of the reflow profile; speeding up or slowing the conveyor results in altered temperature profiles.
The pre-flow or soak and the ramp-up section, also called the flux activation stage, brings the entire assembly up to the temperature at which the flux activating and the alloy in the paste changes its phase from solid to liquid. This soak time should be long enough to allow the flux to clean the surfaces, but not so long that the flux is evaporated prematurely.
During the reflow phase, the temperature increases further to melt the solder alloy and subsequently, intermetallic layer will form at the boundary surfaces. The typical peak temperature is 30–40 °C higher than the solder alloy melting point. It is important to monitor the time at peak reflow temperature in several areas of the PCB.
In the cool down phase, a reliable solder joint is formed. To obtain a strong joint between the solder pad and the components' terminal, the cooling should be fast. A lower rate may increase the grain size of the intermetallic compounds making the solder joint brittle and weak. On the other hand, the components can crack if the temperature drops too rapidly. The cooling rate should therefore be 3–4 °C/s down to around 130 °C. Below 130 °C the cooling rate is not critical to the solder joint quality; however fast cooling is beneficial for copper OSP board rather than a very slow cooling rate. The solderability will be maintained for second side reflow, wave or selective soldering. Conveyor speed is a critical affecting parameter of the reflow profile; speeding up or slowing the conveyor results in altered temperature profiles.
Reflow ovens
The reflow ovens can be classified in two ways, by the mean of heat transport method and by the mean of circuit board transportation. By the mean of heat transportation, we distinguish between IR heating and convection heating. By the means of circuit board transportation, we distinguish between batch reflow ovens, and conveyor reflow ovens. In the case of IR heating, the ΔT can be large, therefore forced convection ovens are used mainly in the industry.
Batch reflow ovens mainly applies IR heating and only 1 heating zone exists. Their features are:
- Small size
- Off-line machines
- Low capacity
- Used for small series
- Appropriate for simple assemblies

In the case of conveyor ovens, the assembly travels through separated heater zones. The temperature of the zones can separately be controlled. Therefore, the thermal profile is controlled by the heater zone temperatures and the speed of the conveyor. The ΔT can be low! Conveyor ovens typically contains 3–14 heater zones.
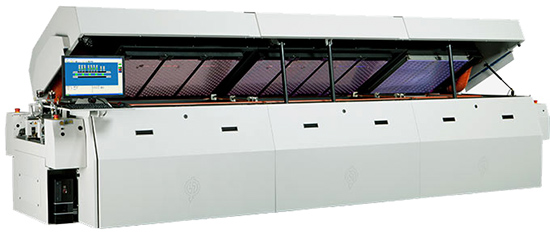
Previous | Next |