
2 - Soldering methods, solder joint design
2.1 - Principles of solder joint design
Definition of soldering
Soldering is a fixed-by-material type joint: the joint between the elements is fixed by a material, the solder, with lower melting point than that of the elements. The solder is melted, it wets the surfaces, and the joint is formed when the solder is cooled down and re-solidifies. The type of solders depends on the applied solderging technology. It is: solder wire for hand soldering; solder bar for wave soldering and solder paste for reflow soldering.
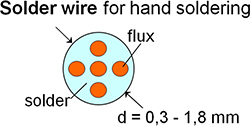
Typical solder alloys:
- lead free, e.g. a SAC alloy: 95.5Sn/3.8Ag/0.7Cu; melting point 217 °C
- eutectic tin-lead alloy: 63Sn/37Pb; melting point 183 °C
Type of fluxes to promote solder spreading and wetting of the contact surfaces:
- resin of fir tree: soluble in alcohol, non-corrosive, inclined to oxidation, hard to clean (remove), most popular
- RMA – Rosin Mildly Activated: slightly activated (treated by acid) resin, or its synthetic equivalent
- no-clean flux: transparent, the board does not need cleaning
- water soluble organic compounds
Solder joint design
Model and design of a solder joint
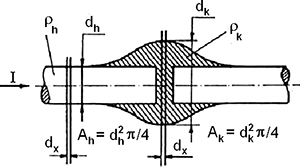
A joint is proper, if:
Two solder joints with standard design parameters:
Wire lead soldered to a pad![]() |
Gull wing lead soldered to a pad ![]() |
Previous | Next |